Stamping Die Design Secrets
SSP is well known Stamping die manufacturing services provider. Working in this sector for a decades .
Let’s learn about from the very best in the industry.
Stamping Die Design Optimization: Boost Speed & Reduce Defects
Stamping die design is a critical aspect of the manufacturing process that involves creating specialized tools to shape and cut materials into precise parts. This design process helps optimize production efficiency and minimize defects, making it essential for stamping die manufacturing. By focusing on key factors such as material selection, die geometry, and lubrication, manufacturers can significantly enhance the quality and speed of their operations.
For many Chinese manufacturers, implementing advanced design strategies and technologies is vital in achieving high-quality outputs and reducing waste. Effective die design not only streamlines workflows but also ensures that parts meet exact specifications, ultimately leading to faster turnaround times and improved product reliability. Understanding these design secrets is crucial for anyone looking to excel in stamping die manufacturing and gain a competitive edge in the industry.
Fundamentals of Stamping Die Design
Before chasing high-speed runs, it pays to nail the basics. A strong foundation ensures your dies perform reliably, run longer, and produce parts within tight tolerances.
Key considerations include:
Material Selection:
- Hard tool steels resist wear but can be brittle.
- Tougher alloys absorb impact but may dull faster.
- The right balance extends die life without sacrificing precision.
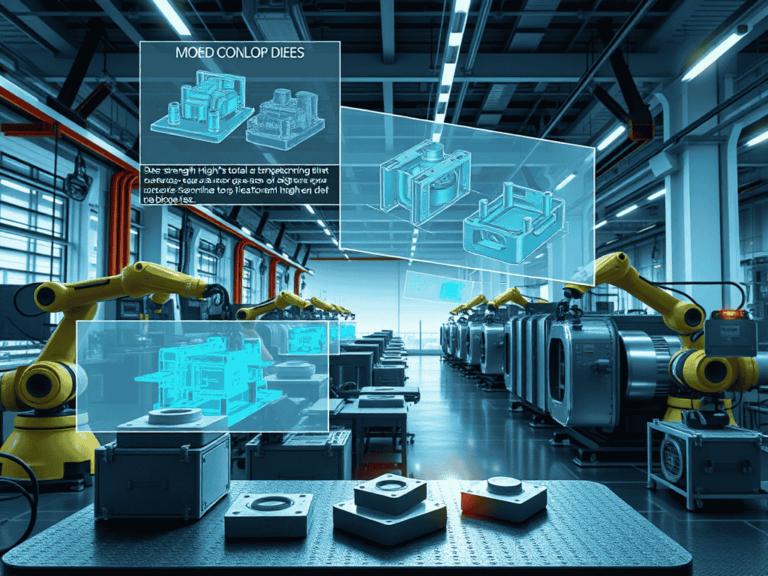
- Core Components:
- Punches, dies, and ejectors must align perfectly.
- Even minor misalignments can cause burrs or part distortion.
- Die Type & Configuration:
- Progressive die stamping merges multiple operations—blanking, piercing, forming—into one continuous flow.
- Blanking dies excel at single-operation cuts.
- Choosing the right die for your part geometry optimizes cycle time.
- Tolerance & Precision:
- Set realistic tolerances based on material behavior and part function.
- Tight tolerances reduce rework but increase tooling cost—find the sweet spot.
Die Design for Faster Production and Higher Efficiency
Speed and efficiency go hand-in-hand when your die is engineered for seamless operation. Small layout tweaks can yield big performance gains.
Try these optimization tactics:
- Streamlined Layout:
- Arrange stations to minimize strip movement.
- Fewer material shifts translate to faster cycles.
- Quick-Change Features:
- Incorporate modular components for rapid die swaps.
- Reducing setup time by even a few minutes adds up over multiple runs.
- Balanced Cutting Forces:
- Distribute load evenly across punches to avoid press overload.
- Balanced forces prolong tool life and stabilize production speed.
- Progressive Die Stamping Advantages:
- Multi-stage dies eliminate manual handling between operations.
- They’re ideal for high-volume, simpler parts—think brackets and clips.
By focusing on layout, changeover, and force distribution, you’ll remove hidden slowdowns and keep your press humming at peak capacity.
Proven Techniques to Reduce Defects in Stamped Parts
Defects not only waste material—they eat into your bottom line and damage your reputation. Address potential problem areas early in the design phase of stamping die manufacturing to ensure every part that leaves your shop meets specifications.
Effective Defect-Reduction Methods:
Root-Cause Analysis:
- Review past runs to identify recurring issues (e.g., burrs, tears, distortions).
- Use that data to adjust die geometry or clearances.
Stress Relief & Venting:
- Integrate relief slots or chamfers to prevent work-hardening and cracking.
- Proper venting helps release trapped air and lubricants, reducing scuffing.
Material Flow Control:
- Optimize strip guidance to feed material consistently into the die.
- Uniform feed prevents uneven deformation and thinning.
Precision Piercing:
- Accurate piercing requires tight alignment between the punch and cavity.
- Consider floating punch holders to compensate for minor press misalignment.
Edge-Conditioning Techniques:
- Polish cutting edges to minimize burr formation.
- Smooth edges mean less secondary deburring and fewer rejected parts.
Applying these techniques at the design stage, especially for Chinese manufacturers, saves time and costs down the line, ensuring high first-pass yields in stamping die manufacturing.
Leveraging Advanced Tools and Technologies in Die Design
The right software and hardware can turn a good die design into a great one—one that virtually guarantees success before the first piece of metal moves.wisconsinmetalparts.com.
Must-have technologies include:
- CAD/CAM Integration:
- Build, tweak, and validate your die designs digitally.
- 3D visualization helps catch interferences and alignment issues early.
- Virtual Simulation & Analysis:
- Simulate material flow, springback, and stress points under real-world loads.
- Early detection of weak zones avoids costly prototype iterations.
- Real-Time Monitoring:
- Fit your dies with sensors to track force, temperature, and cycle counts.
- Data-driven insights enable predictive maintenance, reducing unplanned downtime.
- Advanced Coatings & Materials:
- Apply wear-resistant coatings like TiN or DLC to critical surfaces.
- Use high-strength tool steels or carbide inserts in high-wear regions.
By integrating these cutting-edge tools, you can refine your designs faster, anticipate issues before they occur, and stretch die life well beyond traditional limits
Best Practices for Continuous Improvement in Stamping Die Production
Even a top-performing die can be improved. Establishing a culture of ongoing optimization is vital in stamping die manufacturing, especially for Chinese manufacturers. This approach helps them adapt to changing demands and integrate new technologies. By regularly assessing die performance and gathering feedback, manufacturers can enhance efficiency, minimize defects, and ensure their dies remain competitive and effective in the industry. Continuous improvement is key to long-term success.

Adopt These Best Practices for Stamping Die Manufacturing
Feedback Loops:
- Hold regular debriefs with press operators and quality inspectors.
- Encourage frontline teams to share insights on die performance and part quality.
Preventive Maintenance:
- Schedule inspections based on sensor data and cycle counts.
- Swap worn components before they cause unplanned stoppages.
Cross-Functional Collaboration:
- Bridge the gap between design, toolmaking, and production teams.
- Joint troubleshooting accelerates problem resolution and innovation.
Industry Engagement:
- Attend trade shows, webinars, and professional forums focused on stamping technology.
- Staying current helps you adopt the latest techniques—whether it’s a new die cutting workflow or an emerging coating technology.
By weaving these practices into your daily operations, especially for Chinese manufacturers, you’ll create a feedback-driven environment that constantly refines your dies for maximum performance in stamping die manufacturing.
Conclusion
Designing exceptional stamping dies isn’t a one-and-done project—it’s a journey of continuous learning, strategic innovation, and hands-on collaboration. By mastering the fundamentals of stamping die manufacturing, optimizing your layouts, reducing defects at the source, and embracing advanced technologies, you can transform your production line into a powerhouse of speed and quality.
Now, here’s the question for you: Which design tweak or technology will you implement first? Whether you’re upgrading to progressive die stamping, fine-tuning your piercing accuracy, or integrating real-time monitoring, each step brings you closer to faster cycles, fewer defects, and a healthier bottom line. For Chinese manufacturers, these improvements are crucial for remaining competitive in the global market. Let’s make those enhancements today and watch your parts—and your business—shine.
Check out our manufacturing services
We offer efficient, high-quality manufacturing solutions tailored to your needs, from prototyping to full-scale production, ensuring precision and quick turnaround times.
Check out our SAMPLE PRODUCTS
Discover our quality sample products that highlight our innovation and manufacturing excellence.